Warehouse Softare for Microsoft Dynamics 365 Business Central: Tote Picking
Pick multiple warehouse orders simultaneously and streamline efficiency
Tote Picking
Tote picking in a warehouse refers to a method of order fulfillment and inventory management that involves the use of totes, which are small containers or bins, to organize and transport items within a warehouse or distribution center. This process is commonly used in e-commerce, retail, and other industries where there is a need to efficiently pick and pack products for customer orders.
With the Dynamics 365 Business Central Tote Picker app, warehouse pickers become highly efficient by picking and sorting multiple orders at once, also known as pick-to-tote. Without Tote Picker, pickers would drop off a batch of items at shipping, leaving shippers to sort out which items belong to which orders tediously. With Tote Picker, pickers can use pick carts with dedicated positions or totes to separate the items while they’re picking.
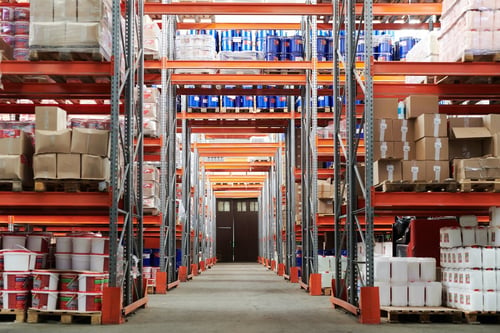
Warehouse Tote Picking Processes
Receiving and Sorting: When products arrive at the warehouse, they are typically sorted and stored in totes or bins. These totes are labeled or tagged with information like SKU (Stock Keeping Unit) numbers, product descriptions, or barcodes to help with identification and tracking.
Storage: The totes are then stored in an organised manner within the warehouse. They may be placed on shelves, racks, or conveyors, depending on the warehouse layout and design.
Order Generation: As customer orders come in, they are processed through Dynamics 365 Business Central. The system generates a list of items that need to be picked and packed to fulfill each order.
Tote Picking: Warehouse workers use handheld devices or computer terminals to receive instructions for picking items from the totes. They may be directed to specific totes or storage locations within the warehouse to retrieve the items required for each order.
Packing: After all the necessary items for an order are collected, they are placed in a separate tote or container designated for packing. This tote may contain packing materials, such as bubble wrap, packing paper, or other protective materials.
Verification: Once the order is packed, it typically goes through a verification process to ensure that all the items are correct, and the order is accurate. This can involve scanning barcodes or checking off items on a checklist.
Labeling: The packed tote is labeled with shipping information, including the customer's address, shipping method, and any other necessary labeling for the shipping carrier.
Shipping: The tote is then sent to the shipping area, where it is prepared for delivery to the customer. This can include labeling the outer shipping box and arranging for the shipment to be picked up by the chosen carrier.
Inventory Management: As totes are used for picking and packing, the warehouse management system automatically updates Sybanics 365 Business Central inventory levels, ensuring that the stock is accurately reflected in the system.
Summary
Tote picking in a warehouse offers several advantages, including increased efficiency, reduced picking errors, and better organisation. It allows for a more streamlined and accurate order fulfillment process, which is essential for meeting customer demands in a timely and accurate manner. Additionally, it can improve the overall flow of goods within the warehouse, leading to better inventory management and cost savings.
Streamline with barcodes
The Tote Picker app leverages barcodes to keep track of multiple orders. Each tote or cart position is equipped with a permanent barcode used to tie an order to the tote.
When an item is picked, the Tote Picker app will direct which tote or position to place the item in and verify the item was correctly placed. With the built-in barcode scanning capabilities, the Tote Picker app ensures pickers select the correct items and put them into the proper totes. If an error is made, Tote Picker will alert the user.
Making packaging and shipping more efficient
With the Tote Picker app, orders are neatly organised in groups enabling those responsible for packaging and shipping to process each order efficiently.
Save time in the warehouse
With the Tote Picker app, workers will decrease the time it takes to pick and sort multiple orders.
Minimize picking errors
As mentioned, barcodes streamline the picking process while reducing errors. As items are picked and scanned, the Tote Picker app will notify warehouse pickers if an incorrect item has been selected. Issues are caught immediately rather than down the line at shipping, or worse, the customer receives the wrong goods.
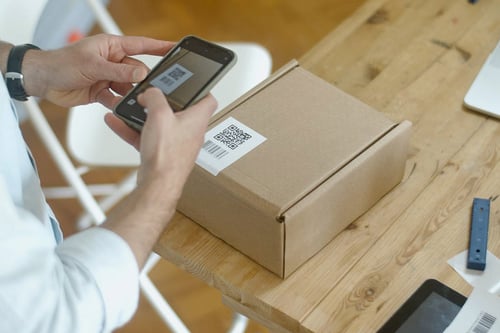